Case Study
3D Printing Turbomachinery for Super Critical CO2 Systems
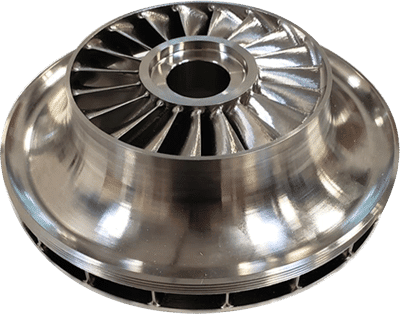
Turbopumps serve as crucial components in various applications, from rocket engines to race cars, where they transform mechanical energy into pressure. At their core, turbopumps feature impellers, available in open or closed (shrouded) designs. Designing these components poses a challenge: striking a precise balance between achieving high fluid velocity and preventing cavitation’s adverse effects, necessitating meticulous blade and channel geometries. Additionally, these parts must endure the rigors of high RPM stresses, often rotating at tens of thousands of RPM.
Recognizing the potential for improvement, Hanwha explored additive manufacturing to streamline the entire turbopump production process, ensuring precise adherence to required specifications. This technology presented an opportunity for accelerated iterations, design refinement, enhanced performance, and optimized functionality.
Finished shrouded impeller designed to enable high RPM with a surface finish optimized to reduce backpressure printed on a Velo3D Sapphire printer.
At a Glance
80% Reduction in Build Time
As compared to conventional metal AM methods, allowing for rapid development and production.
90% Decrease in Support Structures
Significant reduction in support structures, facilitated quicker post-processing and significant cost savings related to material waste.
Cost Savings
Substantial cost savings were achieved by using Velo3D’s Sapphire printer, thanks to reduced material waste, lower labor expenses, and shorter post-processing times, making the additive manufacturing process more cost-effective compared to conventional methods.